UNA FILOSOFÍA DE GESTIÓN: LEAN CONSTRUCTION
- Areli Alvarez Arteaga
- 7 sept 2020
- 7 Min. de lectura
Actualizado: 29 abr 2021

Lean Construction, o "construcción sin pérdidas" es una filosofía de trabajo para la planificación y gestión de proyectos de construcción que nace en los años 90 en Finlandia, teniendo como modelo el Lean Production nacido en la empresa Toyota (Toyota Production System o Lean Manufacturing), aunque luego se aplicó a muchas empresas manufactureras gracias a que se basa en la mejora dentro del sistema de producción, tanto de productos como de servicios, cuyo objetivo fundamental es la identificación y eliminación de pérdidas . Sin embargo, Lean no son una serie de herramientas que se han de aplicar en cualquier lugar, sino que se han de crear nuevas herramientas y sistemas dependiendo de la empresa y del sector.
El Lean Construction focaliza sus esfuerzos en generar valor al producto final, por ello el primer paso es el de eliminar las pérdidas que se generan durante todo el desarrollo de un proyecto de construcción. Ese valor se consigue satisfaciendo las necesidades del cliente y proporcionando bienestar a través de una obra de construcción o edificación para lo cual se han de tener en cuenta muchas variables, incluido el impacto en la sociedad y en el medio ambiente.

Obra de edificación en Brasil donde se presenta públicamente el Planning de Obra.
Por tanto, cada proceso que no genera valor es un proceso que genera un daño al objetivo final, por lo que se considera una pérdida y hay que eliminarlo. Estas pérdidas las clasifica la filosofía Lean en siete:
1. Sobreproducción: Producir por encima de la demanda genera stock, además de que si se produce sin responder a la necesidad del cliente se consumen recursos.
2. Tiempo de espera: Esperar al anterior o al siguiente proceso de producción.
3. Transporte: Transportar productos no necesarios en ese momento para producir el producto final.
4. Exceso de procesado: A causa del diseño o del uso de herramientas de baja calidad la actividad no es eficiente.
5. Inventario o stock: Todo lo que se ha producido y que aún no se ha vendido.
6. Movimiento: Personas o maquinaría moviéndose más de lo necesario para producir el producto final.
7. Defectos: Esfuerzo realizado para investigar sobre los defectos producidos y tener que arreglarlos.
En conclusión, la filosofía Lean se podría resumir en los siguientes principios:
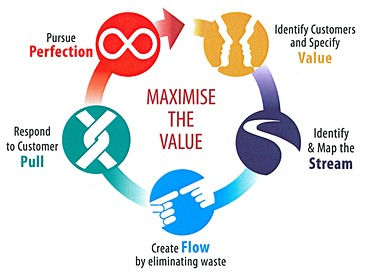
Reducción de las actividades que no agreguen valor.
Incremento del valor de la producción a través de una consideración sistemática de los requerimientos del cliente.
Reducción de la variabilidad.
Reducción del tiempo de los ciclos.
Simplificación mediante la reducción de pasos, partes y relaciones.
Incremento de la flexibilidad del producto terminado.
Incremento de la transparencia de los procesos.
Enfoque en el control de los procesos completos.
Introducción de procesos de mejora de los flujos con la mejora de las conversiones.
Referenciar los procesos con los de las organizaciones líderes (benchmarking).
Organización de la producción como un flujo continuo.

Búsqueda de la perfección: entregar un producto, como lo requiere el cliente, sin pérdida alguna.
A continuación veremos algunas herramientas para aplicar la filosofía Lean a cualquier proyecto.
LAST PLANNER SYSTEM o SISTEMA DEL ÚLTIMO PLANIFICADOR
Este sistema ayuda a dirigir las relaciones entre los participantes en el proceso, la comunicación entre ellos y sus promesas, donde colaborando juntos son capaces de tomar decisiones sobre el planning inicial y el de producción al nivel más bajo posible.
El Last Planner System, .añade un componente de control de producción al sistema de gestión de proyectos tradicionales, entendiéndose como un mecanismo para la transformación de lo que debe hacerse en lo que se puede hacer, formando así un inventario de obra semanal. Las actividades se les denomina asignaciones y son un compromiso por parte de los últimos planificadores (capataces, encargados, etc.) sobre lo que realmente van a hacer. El objetivo de este sistema es el de generar una planificación realista, en lugar de una irreal y muchas veces optimista.

Todo esto se realiza gracias a la colaboración entre los agentes de la siguiente forma:
DEBERÍA: Primero se fijan los objetivos globales teniendo en cuenta las restricciones fundamentales del proyecto.
PUEDE: Se utilizan esos objetivos para planificar procesos más detallados y se especifican los medios necesarios para conseguir los objetivos
SE HARÁ: Se eliminan las restricciones y el último planificador decide que hará, y se compromete a ello, al día o semana siguiente.
Además de tener la planificación inicial, que es la que solemos usar actualmente a la que llamamos Plan Maestro o Master Plan, se realizan planificaciones intermedias, planificaciones semanales y se realiza un seguimiento de lo planificado gracias al indicador PAC (Porcentaje de Asignaciones Completadas).
PLAN MAESTRO: Se le denomina así al planning inicial, donde se hace hincapié en los hitos demandados por el cliente o por alguna otra causa.
PLANIFICACIÓN INTERMEDIA: Viene después del plan maestro y precede a la planificación semanal basada en el compromiso. Esta planificación tiene una visión de entre 4-6 semanas y es adaptable a las necesidades y características del proyecto. En esta fase se detallan más las actividades a ejecutar así como las subtareas para su ejecución, y que pueden entenderse como prerrequisitos de trabajo, directrices o recursos necesarios para su realización, que se conocen como restricciones. Una vez éstas se determinan, las actividades deben someterse al proceso de preparación, donde las restricciones son eliminadas, dejando la actividad lista para ser ejecutada.
PLANIFICACIÓN SEMANAL: El Sistema del Último Planificador pretende incrementar la calidad del Plan de Trabajo Semanal (PTS), el cual cuando se combina con el proceso de planificación intermedia genera el control del flujo de trabajo.
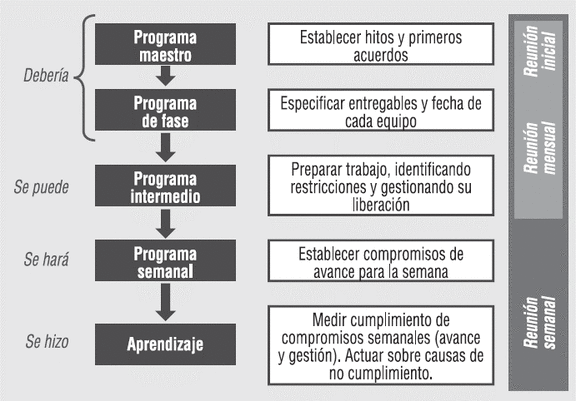
Como ya se ha indicado, el Sistema del Último Planificador necesita medir el desempeño de cada plan de trabajo semanal para estimar su calidad, que es el primer paso para aprender de los fallos e implementar mejoras. Esto se realiza a través del Porcentaje de Asignaciones Completadas (PAC), que es el número de asignaciones completadas programadas divididas por el número de asignaciones programadas para una semana dada. De esta manera, el PAC evalúa hasta qué punto el sistema del último planificador fue capaz de anticiparse al trabajo que se haría en la semana siguiente, es decir, compara lo que será hecho según el plan de trabajo semanal con lo que realmente fue hecho, reflejando así la fiabilidad del sistema de planificación. Un buen logro ejecución se sitúa por encima del 80%; un logro pobre está por debajo del 60%.
Con todo ello podemos decir que Last Planner System es una herramienta muy útil para mejorar la confiabilidad y rebajar la incertidumbre en la planificación. La planificación intermedia, el plan de trabajo semanal y las reuniones de control de lo planificado afectan positivamente el desarrollo de la obra en diferentes aspectos:
Comunicación, ya que la planificación intermedia y el plan de trabajo semanal se realiza conjuntamente en la obra.
Compromiso, al ser tenidos en cuenta para la planificación los agentes que intervienen directamente en el desarrollo de la misma (últimos planificadores).
Cultura de medición, necesaria para establecer referencias del desempeño del proyecto.
Mejora continua, una vez establecido el indicador PAC de cumplimiento de lo planificado, la herramienta se aplica sistemáticamente.
Con el nuevo sistema, el papel del jefe de obra se torna proactivo , ya que es necesario analizar y levantar las restricciones de las actividades para definir las asignaciones de trabajo de la unidad de producción.
El análisis de las causas de no cumplimiento de lo planificado ofrece una importante información, utilizada para evitar la recurrencia de situaciones que generan atrasos y baja productividad en la obra.
LEAN PROJECT DELIVERY SYSTEM
Uno de los problemas más frecuentes en todos los proyectos es su indefinición, ya que en muchas ocasiones no hay otra forma de hacer los proyectos que indefinidos en algunos aspectos, debido a que en la fase de redacción no se sabe quien lo va ejecutar, qué sistemas utilizará e incluso que materiales se emplearán finalmente, por lo que es normal que el proyecto no pueda entregarse con una definición absoluta. Por todo ello el Lean Project DeliverySystem trata de mejorar el sistema integrando la fase de diseño con la de producción al incluir a todos los agentes desde la fase de diseño, de esta forma todos van entendiendo las necesidades del cliente y como poder satisfacerlas a la vez que son capaces de desarrollar una solución efectiva en la relación coste-producción.
Este sistema nos ofrece unos beneficios potenciales para poder mejorar el actual:
Facilidad para unificar las opciones del diseño con los objetivos del negocio.
Mejorar el valor y elevar la calidad del producto.
Minimizar el coste de construcción y de operaciones al considerarse la logística desde el principio.
Entrega rápida de la instalación y recuperación de la inversión antes.
Mayor definición y menor repetición de trabajos, por tanto menor coste y finalización más rápida.
Gestión de forma sistemática de las relaciones, conversaciones y compromisos.
Mayor facilidad para crear edificios respetuosos con el medio ambiente.
Mayor exactitud en el proceso constructivo y certeza en el coste.
Reducción en el tiempo de redacción de documentos.
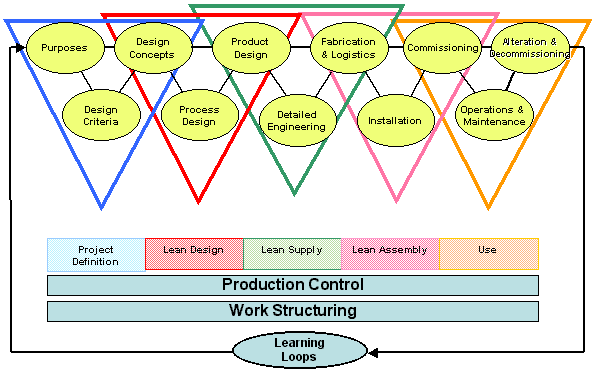
OTRAS HERRAMIENTAS
Set-Based Design.
Esta herramienta ofrece la posibilidad de desarrollar posibles soluciones a los problemas durante la fase de diseño y producción del producto y decidirlo en el momento adecuado (momento responsable), permitiendo al equipo de diseño desarrollar varias opciones de diseño en paralelo y escoger la más adecuada con el acuerdo entre el resto de agentes, reduciendo la necesidad de rehacer trabajos a última hora.
Evidence-Based Design.
Evidence-based design (EBD) es una herramienta útil para conectar el diseño con los objetivos de la propiedad, usando datos reales para influir en el diseño. Sobre todo se utiliza en arquitectura para hospitales, ya que se ha comprobado que el entorno, la luminosidad, el espacio, etc., influyen en la recuperación de los pacientes.
Target Value Design.
El Target Value Design (TVD) está basado en la estrategia comercial del Target Costing, donde se fija un precio de referencia de mercado y se trata de disminuir ese coste a través de la colaboración de todos los agentes, así se incentiva a los agentes para disminuir el precio de referencia tomado de las bases de datos de las propias empresas o de las instituciones dedicadas a ello. Value Stream Mapping. Value Stream Mapping (VSM) es un gráfico que representa el flujo de un proceso para generar valor. Se analizan los procesos diferenciando las tareas que generan valor y las que no lo hacen con el objetivo de reducir el tiempo de ejecución.
CONCLUSIONES Debido al aumento de la competencia y de la especialización cada vez se hace más necesario optimizar al máximo todo lo que conduzca a crear valor en cada proyecto, satisfaciendo las necesidades del cliente, mejorando la calidad y la productividad y reduciendo el coste y el plazo. Todo ello se puede conseguir por los diferentes métodos de gestión que existen, como el propuesto por el Project Management Institute (PMI), pero a diferencia de éstos, Lean Construction no es una metodología sino una filosofía focalizada en la producción, usando unas herramientas que se han de adaptar, e incluso crear nuevas, dependiendo del país, empresa o proyecto.
FUENTES:
Lean Construction Institute.
F, CERVERO ROMERO. Lean Construction: nueva filosofía de gestión en la construcción española.
TRANSCRIPCIÓN: Areli Álvarez Lean Construction México®